Table of Contents
What is a Plasma Cutter and How Does it Work?
Claire Posted on Mar 03, 2020
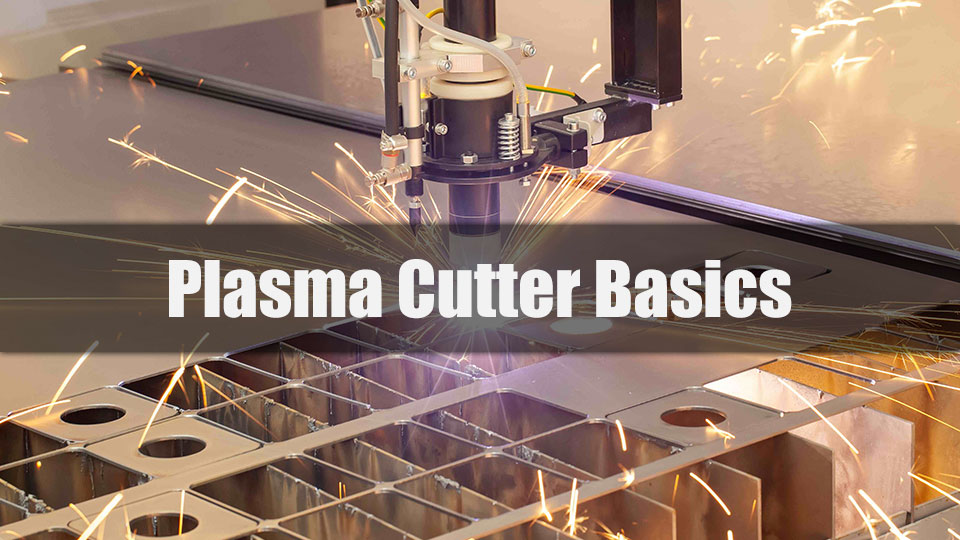
What is a Plasma Cutter?
A plasma is a state of matter like a solid, liquid or gas. Adding heat to material causes the molecules in it to vibrate or move more quickly. When a solid is heated, the molecules start to vibrate more vigorously. Eventually the solid turns to a liquid and the molecules actually move around and collide with each other. As more energy or heat is added the motion becomes faster and more vigorous still and eventually the molecules move so quickly and collide so energetically (violently) that they separate and form a gas. If still more energy is added to the gas the molecules travel faster and thus collide with each other more violently and the gas changes to a plasma.
In simple terms, a plasma cutter is a tool that can cut through various types of electrically conductive materials, namely metals such as steel, copper, brass, aluminium and others. It does this by creating a high-temperature, electrical channel of ionized gas, which is known as plasma. There are different types of plasma cutters from small, hand-held machines that are used by home hobbyists to large, automated CNC cutters used by various industries.
Plasma cutters can be found in all shapes and sizes. Today, it is not uncommon to find huge plasma cutters that work through robotic arms in order to make precise cuts and incisions to very compact, hand-held plasma cutters found in many handyman shops. Regardless of how big or complicated they are, all plasma cutters function on the same principle, and they are all basically constructed around the same design.
The term "plasma cutter" is actually a broad term. These machines are composed of several individual components. The design and material-quality of each component factors into price, with higher quality components costing more. This does not mean that low-priced cutters are undesirable, especially for hobbyists and such, but it does mean that higher priced cutters will often be able to perform more heavy-duty tasks than lower priced ones and often come with more features.
How Does a Plasma Cutter Work?
The vast majority of plasma cutting systems today can be grouped into either conventional or precision categories.
Conventional Plasma Cutters
Conventional plasma systems typically use shop air as the plasma gas, and the shape of the plasma arc is basically defined by the orifice of the nozzle. The approximate amperage of this type of plasma arc is 12-20K amps per square inch. All handheld systems utilize conventional plasma, and it is still used in some mechanized applications where the part tolerances are more forgiving.
Precision Plasma Cutting Systems
Precision plasma systems (high current density) are designed and engineered to produce the sharpest, highest quality cuts that are achievable with plasma. The torch and consumable designs are more complex, and additional pieces are included to further constrict and shape the arc. A precision plasma arc is approximately 40-50K amps per square inch. Multiple gases such as oxygen, high purity air, nitrogen, and a hydrogen/argon/nitrogen mixture are used as the plasma gas for optimum results on a multitude of conductive materials.
Handheld Operation
In a typical handheld plasma system, the electrode and nozzle consumable parts are in contact with one another inside the torch when in the OFF state. When the trigger is squeezed, the power supply produces a DC current that flows through this connection, and also initiates the plasma gas flow. Once the plasma gas (compressed air) builds up enough pressure, the electrode and nozzle are forced apart, which causes an electrical spark that converts the air into a plasma jet. The DC current flow then switches from electrode to nozzle, to a path between the electrode and work piece. This current and airflow continues until the trigger is released.
Precision Plasma Operation
Inside a precision plasma torch, the electrode and nozzle do not touch, but are isolated from one another by a swirl ring which has small vent holes that transform the preflow/plasma gas into a swirling vortex. When a start command is issued to the power supply, it generates up to 400VDC of open circuit voltage and initiates the preflow gas through a hose lead set to the torch. The nozzle is temporarily connected to the positive potential of the power supply through a pilot arc circuit, and the electrode is at a negative.
Next, a high frequency spark is generated from the Arc Starting Console which causes the plasma gas to become ionized and electrically conductive, resulting in a current path from electrode to nozzle, and a pilot arc of plasma is created.
Once the pilot arc makes contact to the work piece (which is connected to earth ground through the slats of the cutting table), the current path shifts from electrode to work piece, and the high frequency turns off and the pilot arc circuit is opened.
The power supply then ramps up the DC current to the cutting amperage selected by the operator and replaces the preflow gas with the optimum plasma gas for the material being cut. A secondary shielding gas is also used which flows outside of the nozzle through a shield cap.
The shape of the shield cap and the diameter of its orifice forces the shield gas to further constrict the plasma arc, resulting in a cleaner cut with very low bevel angles and smaller kerf.
What are the Advantages of Plasma Cutting?
Plasma cutting is an excellent choice for most cutting applications but it is particularly well suited for applications where speed and excellent cut quality are important. Because of the intense heat of the plasma arc – around 40,000°F (22,000°C) compared to 5,700°F (3150°C), with gases used with Oxy-Fuel torches – the cut is very clean with little or no dross.
The plasma cutter also cuts ferrous and non-ferrous metals much faster than an Oxy-Fuel torch or abrasive saws, with low or no heat affected zone, especially on thinner metals. A clean cut with little or no dross means less time and money is required to finish the work piece. Parts are virtually weld-ready.
With plasma cutting, less preparation work is required. A plasma arc is hot enough to burn through most surface coatings such as paint and rust and still provide excellent cutting results.
For applications where difficult shapes are being handled or cut, such as ventilation ductwork (HVAC), tanks or vessels, plasma cutting offers a considerable advantage since no fixturing is required. All you need is a place on the metal to attach the work clamp. And with plasma cutting, there is also minimal heat input and distortion of the metal as there is with jigsaws or cutting shears.